Metal Matrix Composites: Classification, Manufacturing, and Application
- World Scholars Review
- Sep 3, 2023
- 18 min read
Updated: Oct 19, 2024
Author: Hayato Nagai
Mentor: Dr. Francesco De Cola (PhD, University of Oxford). Dr. De Cola is Head of Design and Engineering for Advanced Projects at McLaren Racing
Abstract
Within the last few decades, the popularity of metal matrix composites (MMC) has grown substantially as a response to the universal need for more advanced materials that hold superior properties than conventional metal alloys. The addition of reinforcement materials into the metal alloy matrix produces the superior properties that MMCs hold. Along with the description of the different types of matrices and reinforcement, this paper delves into the important factors that affect the properties of MMCs such as material compatibility and manufacturing methods. It also presents the impact that MMCs have made across industries and defines the main manufacturers, producers, and research that have led to the increase in the adoption of MMCs.
Introduction
Composites are the combination of two or more physically and chemically distinct materials that result in electrical, thermal, chemical, and physical properties drastically different from their constituents. Such base constituents are generally defined as matrices and reinforcements. The matrix is the base material that consists of either metal, ceramic, or polymer and makes up the majority of the composite in volume. The reinforcement - which can be either fibers (long or short), particles, or whiskers - is the material encapsulated into the matrix that provides superior load bearing capability. The matrix bonds the reinforcements together and transfers the applied load to them. Composites are used in very demanding mechanical applications as they provide specific mechanical properties (e.g. strength, stiffness, etc.) higher than what is offered by the matrix material alone. Based on the type of material used for the matrix, composites are generally classified into three categories:
●Metal matrix composites, which use metals such as aluminum, copper, magnesium, titanium, cobalt as the matrix (Sharma et al., 2020, 2420)
● Ceramic matrix composites, which use ceramic materials such as alumina, silicon carbide, aluminum nitride, silicon nitride or zirconia as the matrix (Cho et al., 2009, 1934).
● Polymer matrix composites, which use either thermosets or thermoplastics as the matrix (Bleay et al., 2001, 1767).
Polymer matrix composites (PMC) are so defined because they adopt a polymeric matrix. Examples of thermoset materials that are commonly used in PMCs are epoxies, phenolics, polyurethanes, and polyimides. Of these, epoxy systems currently dominate the advanced composite industry (Bleay et al., 2001, 1767). Thermoplastic matrices are beginning to be used in engineering applications. Unlike thermosets, thermoplastics can usually be reheated and, if desired, reformed into another shape. Examples of thermoplastic resins used in advanced applications are Polyether ether ketone (PEEK), Polyetherimide (PEI), Polyetherimide (PEI), and Nylon. Both types of polymeric matrices are then paired with either long or short fibers, usually ceramic, carbon, boron, metallic, polymeric, or natural fibers. PMCs offer very high specific mechanical properties and good corrosion resistance (Bleay et al., 2001, 1767). Moreover, they are more affordable than the other two classes of composites. However their operational temperature range is quite limited (only up to 300 degrees C) and they suffer from moisture absorption from the environment, which causes swelling in the polymer as well as a decrease of glass transition temperature. Finally, the adoption of drastically different materials for the matrix and reinforcement produces a thermal mismatch between polymer and fiber that may cause cracking or debonding at the interface (Zhao et al., 2006, 5450).
The second class of composites are ceramic matrix composites (CMC), which are composed of ceramic fibers dispersed into a ceramic matrix. They were first developed to overcome the very low fracture toughness that characterize the ceramic materials. The adoption of ceramic fibers dispersed in the ceramic matrix results in the increase of the energy needed for crack propagation, thus resulting in an increase of the fracture toughness of the composite (Cho et al., 2009, 1934). CMCs are used in engineering applications where high temperatures are expected (heat shields in aerospace applications, engine components, brakes, etc.) as they are able to operate at temperatures up to 1000 deg Celsius. Moreover, depending on the type of ceramics used, their electrical and thermal properties can range from good insulators to excellent conductors (Yamamoto, 2012, 2009).
Metal matrix composites (MMC) are a class of materials made up of a metal matrix reinforced with other metal or ceramic inclusions. Although the reinforcement can vary, the matrix within the MMC itself is either a pure or alloy metal. Common reinforcement materials used in MMCs include alumina, silicon carbon, carbon, and boron fibers (Rajan et al., 1998, 3491).
In comparison to polymer matrix composites (PMCs), MMCs hold an advantage due to their higher operating temperatures, higher transverse stiffness and strength, and higher electrical and thermal conductivity. MMCs are also non-flammable, do not suffer from moisture absorption or outgassing and have better radiation resistance (Sharma et al., 2020, 2420).
When compared to CMCs, despite having lower operating temperatures (see Figure 1), MMCs hold an advantage in strength, density, and elasticity, which puts MMCs in between PMCs and CMCs in terms of mechanical performances.
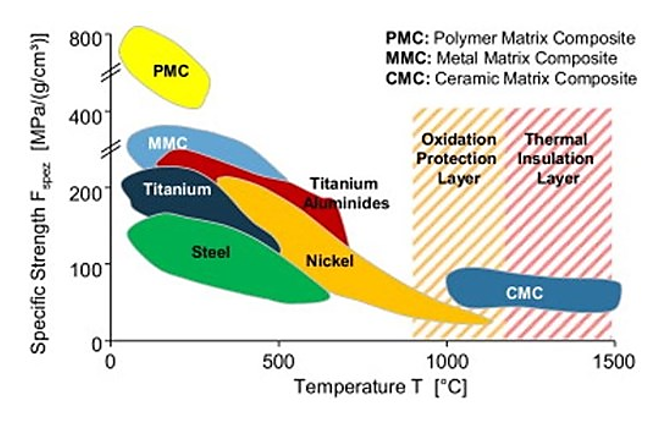
Figure 1: A graph comparing the specific strength and operating temperatures of MMCs, PMCs, and CMCs (Gardiner, 2017)
MMCs are currently adopted in very demanding environments across the world. However, these effective materials also come with some disadvantages, including low sustainability due to the high embodied energy, difficulty in recycling after their end of life, high manufacturing costs, and limited supply chain (Sharma et al., 2020, 2420). The aforementioned disadvantages have, to date, limited the adoption of such materials in certain industries. However, metal matrix composites are seeing substantial market growth and demand from the aerospace and automotive industry, with researchers predicting that the growth rate will reach 11% by 2025 (Point of Use Water Treatment Systems Market, Global Industry Size Forecast Report, n.d.).
This paper reviews the state of the art of MMCs, by thoroughly examining the types of matrices and reinforcements used in the metal matrix composites, the ways in which MMCs are manufactured, and their main engineering applications.
Literature Review
Types of Matrices Used in Metal Matrix Composites
Within the MMC, the matrix is a continuous monolithic material into which the reinforcement is embedded. It is usually a lighter metal such as aluminum, magnesium, or titanium, and provides a complete support for the reinforcement. In high-temperature applications, cobalt and cobalt-nickel alloy matrices are used (Behera et al., 2019, 159). Despite its low popularity in the early stages of development of MMCs, it is now one of the most prevalent materials in the market (Nturanabo et al., 2019).
Aluminium Matrix
The popularity of aluminum is due its easy handling and malleability, low weight, high strength, high corrosion resistance, and high volume of methods of production. Aluminum presents a low melting temperature and therefore has poor performance at high temperatures. It has low hardness along with very low wear resistance, but shows good thermal and electrical properties. These traits of aluminum and its alloys are what make it highly desirable as the matrix for MMCs, where the addition of a reinforcement increases the resulting tensile strength, melting temperature, thermal stability, and mechanical characteristics. These characteristics of aluminum makes it one of the most highly sought materials for the matrix. These aluminum MMCs are currently used in automotive, motorsport, and aerospace applications because of their lightweight. Aluminum is commonly paired with ceramic reinforcements to further decrease its weight as well as enhance thermal, mechanical, and tribological characteristics (Sharma et al., 2020, 2419).
Magnesium Matrix
The common usage of magnesium as matrix in MMCs can be traced back to its characteristic low density, which is approximately two-thirds of that of aluminum (Dey & Pandey, 2015, 58). Magnesium alloys are widely used in automotive and aerospace applications. However, magnesium alloys also exhibit poor creep resistance at high temperatures, low strength, low modulus, and low wear resistance. These limiting factors can be overcome with the adoption of reinforcements. Magnesium MMCs present many advantages over monolithic magnesium and other magnesium alloys, such as higher elastic modulus, higher strength, higher wear resistance at elevated temperatures, and superior creep properties (Dey & Pandey, 2015, 58-59).
Titanium Matrix
Another lightweight alternative for the matrix of a MMC is Titanium. Its highly specific strength and stiffness offers superior weight reduction even at high temperatures when compared to monolithic superalloys (Hayat et al., 2019, 418). Furthermore, titanium MMCs can also offer up to 50% weight reduction compared to these monolithic superalloys at high-temperatures while also maintaining the equivalent strength and stiffness. Titanium and its alloys hold excellent chemical resistance and biocompatibility, which prove to be unique characteristics required in a wide range of applications, including marine and biomedical applications (Hayat et al., 2019, 418-419).
Types of Reinforcements Used in MMC
Reinforcements are used in metal matrix composites and composites of all types to enhance the performance by sharing the load applied upon the matrix. Within a composite, the ideal principal mechanical, thermal, physical, and tribological properties are defined as a function of those of each constituent via the rule-of-mixture (Rohatgi, 1993, 325):

where Pc is the resulting property for the composite, Pm and Vm are the considered property of the matrix material and the volume fraction of the matrix respectively, and Pf and Vf those of the reinforcements.
The three most common types of reinforcements used in MMC are: continuous fibers, whisker short fibers, and particles – each come with their own beneficial traits and uses. A graphical representation is included in Figure 2.
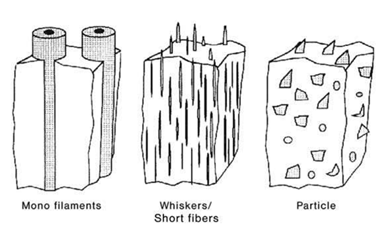
Figure 2: Image representing the three types of reinforcements (Kainer, 2006, 4)
Continuous Fiber Reinforcement
Continuous fiber reinforced MMCs consist of relatively fine fibers, either unidirectional or woven, usually made of aluminum, silicon carbide, titanium bromide, or carbon. The use of continuous fiber reinforcements result in high tensile strength for the composite in the direction of the fibers. This makes them suitable for applications where structures are exposed to very high mechanical loading. However, because of the complex and expensive process of manufacturing continuous fiber MMC and partially due to its limited ability to produce a range of shapes, alternative reinforcement types are being looked at (Nturanabo et al., 2019).
Whisker Fibres
Whisker fiber, or short fiber reinforcements are non-continuous fibers that hold an aspect ratio greater than 5 and are frequently made of silicon carbide or aluminum oxide. Although they are generally cheaper then their continuous reinforcement counterpart, they show high isotropy in exchange for low strength. Moreover, because of the very fine size of the reinforcement, concerns for health hazards have lowered their usage (Nturanabo et al., 2019).
Particle Reinforcement
Generally referred to as particulate reinforced MMCs, particle reinforcements generally contain equi-axed ceramic reinforcements with an aspect ratio of less than 5 and volume fraction of less than 30%. Due to the thermal mismatch strain present between the matrix and the particle reinforcement (also known as the interface), particulate reinforced MMCs hold a much higher toughness and strength (Nturanabo et al., 2019). The main materials used as particle reinforcements are silicon carbide and aluminum oxide. Silicon carbide is used because of its ability to increase tensile strength, hardness, density, and wear resistance. Aluminum oxide, on the other hand, provides good compressive strength as well as wear resistance. Some other reinforcement materials include boron carbide, fibers, zircon, and fly ash.
Boron carbide, being one of the hardest known elements, increases hardness and elasticity but not wear resistance. Zircon, a hybrid reinforcement consisting of particles and fibers, increases wear resistance substantially. Fly ash increases the electromagnetic shielding effect of aluminum MMCs and it is commonly adopted due to its low cost and because it is a waste-by-product in thermal power plants (Ramnath et al., 2014, 55).
Fiber to Matrix Compatibility
The combination of dissimilar materials used for reinforcements and matrices does not come without problems or limitations. Most of these occur at the interface between the matrix and the reinforcement. Wettability is a common concern when merging a molten metal matrix and a solid reinforcement which are physically and chemically dissimilar. Wettability measures how well a solid is covered by a liquid and it is generally measured by the contact angle, as indicated in Figure 3. If the contact angle is less than 90 degrees, the liquid has wet the solid (high wettability); otherwise, solid and liquid substrates do not interact. Low wettability results in a weak interface between reinforcement and matrix and, in turn, in lower resulting mechanical performances of the composite. This is generally due to surface chemistry and surface tension (Hashim et al., 1999, 3-4).
To improve the wettability of a reinforcement, the chemistry of the particle surface - which includes all contaminations and oxidations - the melt surface, and the oxide layer must be taken into account. Techniques often used to improve wettability of MMCs include metallic coatings on the reinforcement and addition of reactive elements (i.e. magnesium, calcium, and titanium) to the melting and heating phases of the matrix before the addition of the reinforcement (Hashim et al., 1999, 4). The increase of wettability is achieved by either increasing the surface energy of the solid, or decreasing the solid/liquid interfacial energy, or by decreasing the surface tension of the liquid, as indicated by the Young Dupre’s equation (Rajan et al., 1998, 3492):

with all the subscript as defined in Figure 3.
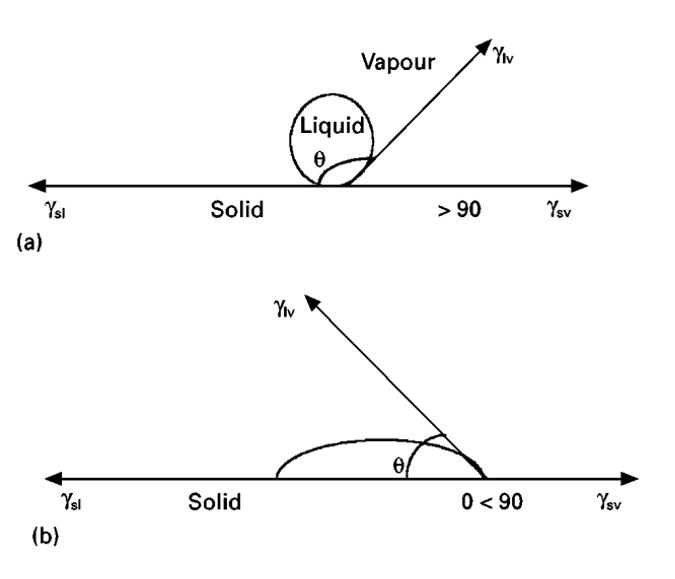
Figure 3: Illustration of the contact angle in a (a) non-wetting interface and (b) wetting interface (Rajan et al., 1998, 3492)
In cases where chemical reactions occur at the interface between the matrix and reinforcement, another layer of material is formed. These interfacial reactions can sometimes decrease the interfacial energy of the metal/reinforcement interface and improve adhesion and wettability. In other cases, the reverse is completely possible, leading to less wettability. Coating of the reinforcement is also a way of preventing the interfacial reaction (Rajan et al., 1998, 2).
Manufacturing Methods for MMCs and Main Producers
Manufacturing methods used to produce MMCs can be broadly categorized in two main types of processes: (1) liquid state processes and (2) solid state processes. Some of the more notable methods over the past few years include powder metallurgy, stir casting, squeeze casting, and spray deposition, as indicated in the graph shown in Figure 4 (Reddy et al., 2020, 83).
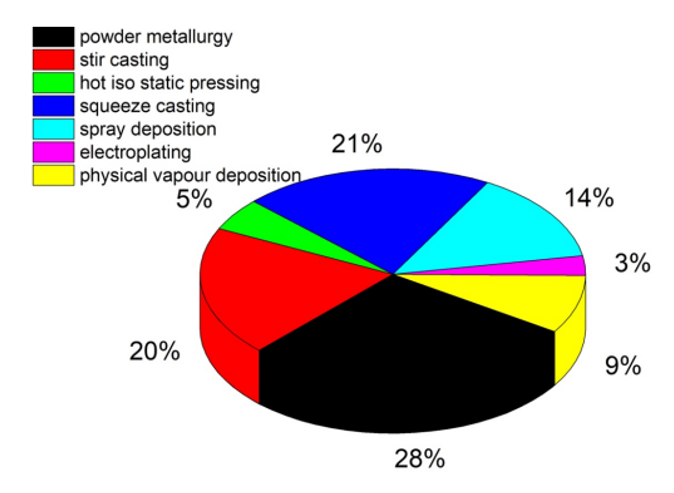
Figure 4: Pie graph with the percentage of the most used manufacturing methods between the years 2005-2020 (Percentage Usage of Various Fabrication Methods During the Past..., n.d.)
Liquid State Processes
Stir casting, also known as liquid metallurgy, is an example of an orthodox liquid-state processing method widely adopted to mass produce MMCs. Its simplicity and low cost makes it the least expensive of all fabrication methods. During the stir casting process, the metal matrix is heated above its melting temperature in a furnace, where a mechanical stirrer plays a crucial role in aiding the addition of the reinforcement material into the molten matrix. An example of schematic for the stir casting process using graphite and argon is shown in Figure 5.

Figure 5: Schematic diagram of the stir casting method (Sharma et al., 2020, 507)
The main drawbacks of stir casting are the lack of uniformity in the distribution of the reinforcement into the matrix, generally due to uneven cooling rates at the surface versus the center, and poor wettability of the reinforcement (Sharma et al., 2020, 508). However, the main limiting factor for molten stir casting, that causes many to look for alternative manufacturing methods, is its ability to only produce metal matrix billets. These rectangular bars must then be further processed before being used in applications. The added steps in the process lowers its ductility and increases wear resistance attributes which, in turn, lowers the machinability and increases the cost and time invested. Yet, stir casting remains the cheapest method for general MMC production.
Squeeze casting is another common liquid state process, in which superheated molten metal is transferred into a close-end die - or a mold - to solidify in its desired shape. One of the two forms of squeeze castings is the direct squeeze casting process, where the squeeze pressure is only provided by the die-closing punch itself. In the indirect squeeze casting process, instead, the squeeze pressure is applied by a secondary ram following the die closing punch. The squeeze casting method produces MMCs that are dense, near net shape, have good surface finish, and have precise dimension (Sharma et al., 2020, 509). However, the squeeze casting process also shows some limitations and requires great process control. For instance, if the metal matrix temperature is too low, porous castings are produced. If the metal matrix temperature is too high, excessive metal reaction leads to degradation of casting properties (Rohatgi, 1993, 336). Much like stir casting and most of the low-cost liquid state processes, squeeze casting suffers from non-uniformity as well.
Solid State Processes
Spray deposition, which is frequently also referred to as spray forming or spray casting, is a more expensive form of a solid state process (Hashim et al., 1999, 2). In the spray deposition process, molten matrix material is atomized by a gas stream while simultaneously colliding with high velocity with a preheated substrate reinforcement to form a composite. The fairly high solidification rate of the spray deposition process along with the brevity of the contact time between the reinforcement phase and the molten metal reduces substantially the amount of interfacial reactions. As a result, the formation of brittle interfacial phases and the degradation of the properties of the composite is greatly minimized. Spray deposition generates uniform MMCs, despite the absence of a full density. To achieve maximum density, subsequent steps are required to densify the material (Rohatgi, 1993, 337).
With solid state processes, the most common manufacturing method is powder metallurgy. It can produce near net shape MMCs that do not require further processing and is often seen as an alternative to stir casting, along with squeeze casting (Sharma et al., 2020, 507). In the powder metallurgy process, fine metal powders are mixed and blended together, and then degassed in vacuum. The fine powder is then shaped in the desired mould through cold pressing and sintering in a controlled environment (Hashim et al., 1999, 1). Apart from its high costs, this technology saves a considerable amount of time by producing a net shape geometry of the required parts. The production through powder metallurgy also accounts for high strength, dimensional accuracy and minimum scrap loss, along with its efficiency. Although it is efficient for most applications, it can present some difficulties when additional machining of parts is needed (such as for threads, cross bores, or slots), due to the hard and porous nature of the MMC material produced through powder metallurgy (Figure 6) (Behera et al., 2019, 1).
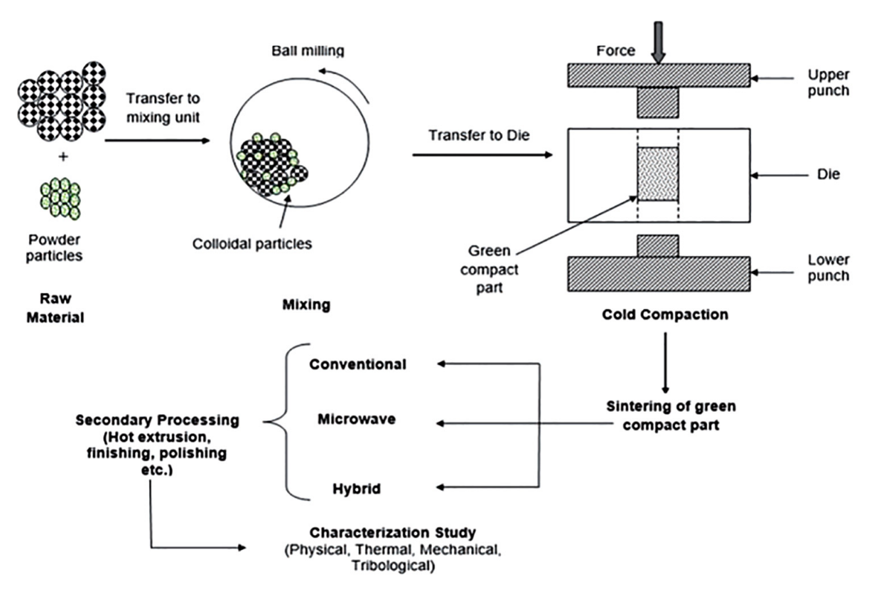
Figure 6: Schematic overview of the powder metallurgy process (Sharma et al., 2020, 512)
Main MMC Producers
In terms of MMC manufacturing, the biggest producer is represented by the United States, mainly for aerospace and defense applications. These aerospace and defense weapon manufacturers include high-tech companies such as Lockheed Aeronautical Systems, Northrup Corporation, General Dynamics Corporation, Boeing Aerospace Company, Textron Specialty Materials, North American Rockwell, and Ford Motor Company (Rohatgi, 1993, 341). However, when looking at the automotive sector, Japan is the main MMC producer. Toyota and Honda, both Japanese automotive companies, mass produce MMCs and have incorporated MMC in various parts of automobiles. Countries across Europe and Asia are also increasing their manufacturing of MMCs, given the massive growth in demand that the market is seeing. Research and Development in MMCs has also increased, with the United States leading the R&D effort. Examples of universities involved are: the University of Wisconsin-Milwaukee, Massachusetts Institute of Technology, University of Virginia, University of Delaware, University of Florida, Carnegie Mellon University, University of Illinois, Michigan State University, Renesslaer Polytechnic, Pennsylvania State University, University of California Santa Barbara and Irvine, University of Alabama, and Witichita State University all having centers on composite materials open since before 1993 (Rohatgi, 1993, 341).
Applications of MMC
The applications of MMCs were first intended for improvements in the avionic and aerospace industry in the mid 1970s. However, as the understanding of MMCs and its usage has grown, its applications have spread out to many other fields of engineering, with more than 80% of MMCs now being utilized for ground transportation (Reddy et al., 2020, 82). In particular, much of the focus has gone towards commercial transportation, with high application potential of MMCs seen in the automotive industry, for devices located in the engine area. An example of a successful implementation of a MMC in car engines is the short-fiber reinforced aluminum alloy piston shown in fig 8. This MMC uses an aluminum-based matrix with a partially-short fiber reinforcement, and in turn strengthens the piston recess range (see Figure 7).

Figure 7: A partially short-fiber reinforced aluminum alloy piston (Kainer, 2006, 49)
MMCs are also used in braking systems of both railways and automobiles. Some more examples of different applications include drive shafts on light load motor vehicles, vented passenger car brake disks, and disk brake calipers for passenger cars (Kainer, 2006, 48). MMCs have been successful at replacing the alloys in automotive because of their benefits in terms of higher specific strength and stiffness, higher temperature resistance, lower thermal expansion, higher wear resistance, and higher thermal conductivity (Kainer, 2006, 51).
Similarly to automotive applications, MMCs have been successfully used in aerospace components to obtain improved mechanical properties, increased component lifetime, improved productivity, increased energy savings, lower maintenance costs, and lower noise levels with fewer airborne emissions. Their applications in engines and other components, much like in automotive applications, have replaced monolithic materials including ferrous alloys, aluminum and titanium alloys, and polymer matrix composites (Nturanabo et al., 2019). In aerospace, both continuous long fibers and discontinuous whisker fiber and particle-reinforced aluminum and magnesium MMCs have been used for frames, reinforcements, aerials, and other joining elements in aerostructures. Examples include the longitudinal bracing beams for planes and fan exit vanes in gas turbine engines as well as rotating blade sleeves in helicopters (Nturanabo et al., 2019). The main goals for these specific implementations of MMCs in aerospace include improvements in strength, stiffness, temperature resistance, thermal expansion, and thermal conductivity. Aluminum MMCs reinforced with a continuous carbon fiber have also been used in aerospace applications such as the structures used in the Hubble Space Telescope, for its ability to provide high dimensional accuracy and high thermal and electrical conductivity without outgassing. Furthermore, the US military has also integrated MMCs into their aviation technology in applications such as ventral fins and fuel access cover doors on military aircraft (Nturanabo et al., 2019).
Along with the adoption of MMCs in both land and air applications, metal matrix composites have also made their way into marine transportation. With weight savings up to 45% when used in ships’ hulls and 65% when used in the superstructure, boats of different shapes and sizes gain an increase in speed and fuel efficiency while lowering maintenance costs (Nturanabo et al., 2019).
Another common application of MMCs is in electrical engineering. The benefits of the adoption of MMCs in electrical applications are due to their higher thermal and electrical conductivity, low thermal expansion, higher weight reductions, and higher strength and stiffness. Examples include electrical contacts and brushes, resistance welding electrodes, sliding contacts and rings, commutators, and superconductors, with the most frequently used matrices for these applications being aluminum, copper, and silver alloys due to their high conductivity (Kaczmar et al., 2000, 62).
MMCs can also be found in sports and recreation. Examples of use in sports products are: golf club shafts and heads, skating shoes, baseball shafts, horseshoes, and bicycle frames (Nturanabo et al., 2019). Similar to what is seen in other fields, MMCs are used in sports products because of their high wear resistance and low weight.
Conclusion
This paper reviews the current knowledge about metal matrix composites and its properties, manufacturing methods, main producers, and application. The increased production and application of metal matrix composites across industries throughout the world can be attributed to its many beneficial properties that could not be attained through its base matrix materials, which commonly include aluminum, magnesium, titanium, and cobalt. Through the addition of reinforcements, which come in either continuous fibers, short whisker fibers, or particles, the base materials see substantial improvements in their traits over its base metal alloy. Common reinforcement materials include silicon carbide, aluminum oxide, boron carbide, fibers, zircon, and fly ash. There are different types of methods to integrate the reinforcement into the matrix metal alloy. In fact, these manufacturing methods are divided into two distinct categories: liquid state processes and solid state processes. These methods mainly include stir casting, powder metallurgy, squeeze casting, and spray deposition. Important factors to be considered in the fabrication of MMCs are the wettability and the interfacial chemical reactions between the matrix and the reinforcement, which come as a result of the combination of two dissimilar materials. Some steps can also be taken to improve the wettability and reduce the interfacial chemical reactions that can cause damage to the properties of the MMCs, such as coating. With the progressive growth of MMCs, manufacturing has become global, with the United States leading in production, research and development, and applications across many industries. Japan is another country progressively increasing MMC production and adoption, especially in the automotive industry. Industries such as aerospace, weapons and defense, automotive, marine, electrical, and sports and recreation have made use of MMCs.
References
Behera, M.P., Dougherty, T., & Singamnemi, S. (2019). Conventional and additive manufacturing with metal matrix composites: a perspective. Procedia Manufacturing, 30, 159-166.
Bleay, S. M., Loader, C. B., Hawyes, V. J., Humberstone, L., & Curtis, P. T. (2001). A smart repair system for polymer matrix composites. Composites Part A: Applied Science and Manufacturing, 32 (12), 1767-1776.
Cho, J., Boccaccini, A. R., & Shaffer, M. S. (2009). Ceramic metal matrix composites containing carbon nanotubes. Journal of Materials Science, 44, 1934-1951.
Dey, A., & Pandey, K. M. (2015). Magnesium metal matrix composites-a review. Reviews on Advanced Materials Science,, 42 (1), 58-67.
Gardiner, G. (2017, April 11). Commercialization of CMCs and developments for next-gen performance. Composites World. Retrieved August 26, 2023, from https://www.compositesworld.com/articles/the-next-generation-of-ceramic-matrix-composites
Hashim, J., Looney, L., & Hashmi, M. S. J. (1999). Metal matrix composites: production by the stir casting method. Journal of Materials Processing Technology, 92, 1-7.
Hayat, M. D., Singh, H., He, Z., & Cao, P. (2019, June). Titanium metal matrix composites: an overview. Composites Part A: Applied Science and Manufacturing, 121, 418-438.
Kaczmar, J. W., Pietrzak, K., & Włosiński, W. (2000). The production and application of metal matrix composite materials. Journal of Materials Processing Technology, 106 (1-3), 58-67.
Kainer, U. K. (2006). Basics of metal matrix composites. Metal Matrix Composites: Custom‐made Materials for Automotive and Aerospace Engineering, 1-54.
Nturanabo, F., Masu, L., & Kirabira, J. B. (2019). Novel applications of aluminum metal matrix composites. In Cooke, K. (Ed.) Alumnum Alloys and Composites, doi: 10.5772/intechopen.86225
Point of Use Water Treatment Systems Market, Global Industry Size Forecast Report. (n.d.). MarketsandMarkets. Retrieved August 26, 2023, from https://www.marketsandmarkets.com/Market-Reports/point-of-use-water-treatment-systems-market-131277828.html
Rajan, T. P. D., Pillai, R. M., & Pai, B. C. (1998). Reinforcement coatings and interfaces in aluminum metal matrix composites. Journal of Materials Science, 33, 3491-3503.
Ramnath, V., Elanchezhian, C., Annamalai, R. M., Aravind, S., & Atreya, T. S. (2014). Aluminium metal matrix composites- A review. Reviews on Advanced Materials Science, 38, 55-60.
Reddy, V. P., Kumar, S. G., Krishnudu, M. D., & Rao, R. H. (2020). Mechanical and wear performances of aluminium‑based metal matrix composites: A review. Journal of Bio- and Tribo-Corrosion, 6 (83), 1-16.
Rohatgi, P. K. (1993, October). Metal-matrix composites. Defence Science Journal, 43 (4), 323-349.
Sharma, A. K., Bhandari, R., Aherwar, A., Rimasausjiene, R., & Bretotean, C. P. (2020). A study of advancement in application opportunities of aluminum metal matrix composites. Materials Today: Proceedings, 26 (2), 2419-2424.
Sharma, D. K., Mahant, D., & Upadhyay, G. (2020). Manufacturing of metal matrix composites: A state of review. Materials Today: Proceedings, 26, 506-519.
Yamamoto, N. (2012). Electrical and thermal property enhancement of fiber-reinforced polymer laminate composites through controlled implementation of multi-walled carbon nanotubes. Composites Science and Technology, 72 (16), 2009-2015.
Zhao, L. G., Warrior, N. A., & Long, A. C. (2006). A micromechanical study of residual stress and its effect on transverse failure in polymer-matrix composites. International Journal of Solids and Structures, 43 (18-19), 5449-5467.
コメント